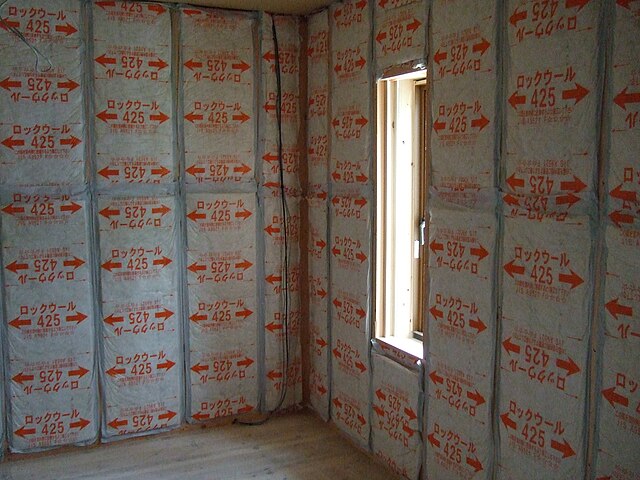
R-Value Explained
R-Value Explained
Energy efficiency in your home starts with understanding R-value, the numerical measure that defines how well a material can resist heat flow. When you're planning your insulation strategy, knowing that higher R-values indicate superior insulating properties becomes your scientific advantage. You'll find this measurement particularly critical in extreme temperatures, where insufficient R-values can lead to significant energy waste and increased utility costs. Your local climate zone determines the optimal R-value needed, with northern regions typically requiring R-49 to R-60 for attics to maintain thermal efficiency. Like the precise calculations in physics, selecting the right R-value requires a methodical approach to achieve maximum effectiveness.
Understanding R-Value Fundamentals
Definition and Basic Concepts
Assuming you're new to thermal resistance concepts, the R-value represents your material's capacity to resist heat flow. When you're dealing with insulation materials, this numerical rating becomes your guide to understanding how effectively a material can prevent heat transfer. The higher the R-value, the greater the insulating power you'll get from your material.
The mathematical relationship between heat transfer and R-value follows an inverse correlation, meaning that as your material's R-value increases, the rate of heat loss decreases. When you're examining different insulation options, you'll notice that manufacturers provide specific R-value ratings based on material thickness, with values typically ranging from R-13 to R-60 for common residential applications.
Your understanding of R-value becomes particularly relevant when you consider that heat naturally flows from warmer to cooler areas. In your building envelope, this principle manifests as heat escaping during winter and infiltrating during summer. The R-value effectively quantifies your material's resistance to this natural heat flow, making it important for energy-efficient building design.
Measurement Units and Standards
The standardization of R-value measurements follows strict scientific protocols that you can rely on for accurate comparisons. In the United States, you'll find R-values expressed in units of ft²·°F·h/BTU, while metric measurements use m²·K/W. For your reference, an R-value of R-38 to R-60 is recommended for attics in most climate zones.
Your insulation choices should align with established building codes and Energy Star guidelines, which specify minimum R-value requirements based on your geographical location. In northern regions, you'll need higher R-values (R-49 to R-60 for attics) compared to southern areas where lower values might suffice.
When you're evaluating insulation products, you should know that testing procedures follow rigorous ASTM International standards. These standards ensure that the R-values you're comparing have been measured under identical conditions, providing reliable data for your decision-making process.
This standardization becomes particularly significant when you consider that R-values are additive. When you layer different insulation materials, your total R-value equals the sum of individual layers, allowing you to achieve higher thermal resistance through strategic combinations.
Importance in Thermal Insulation
Assuming you're planning to optimize your building's energy efficiency, understanding R-value becomes your primary tool for success. Your choice of insulation directly impacts both energy consumption and comfort levels, with proper insulation potentially reducing your heating and cooling costs by up to 50%.
Your insulation strategy should account for different climate zones and seasonal variations. In extreme weather conditions, you'll find that materials with higher R-values provide superior protection against temperature fluctuations, maintaining more stable indoor environments.
When you're selecting insulation materials, you should consider that R-value effectiveness can change over time. Factors like moisture accumulation and compression can reduce your insulation's thermal resistance, making proper installation and maintenance important for long-term performance.
With proper attention to R-value requirements, you can create an energy-efficient envelope that not only reduces your carbon footprint but also provides significant long-term cost savings through reduced energy consumption.
Types of R-Values
There's a diverse spectrum of R-values you need to understand to optimize your insulation strategy. Here are the main types you'll encounter:
- Material-Specific R-Values - Individual insulation materials
- System R-Values - Combined performance of multiple components
- Effective R-Values - Real-world performance measurements
- Cumulative R-Values - Total insulation across layers
R-Value Type | Description |
---|---|
Material-Specific |
Pure thermal resistance of individual materials |
System |
Combined performance of assembly components |
Effective |
Actual performance in real conditions |
Cumulative |
Total R-value of multiple layers |
Assembly |
Overall thermal resistance of complete structure |
Material-Specific R-Values
Assuming you're working with individual insulation materials, you'll find that each has its unique thermal resistance properties. Fiberglass batts typically provide R-13 to R-15 for 2x4 walls, while spray foam can offer significantly higher values per inch.
Your selection of materials will depend heavily on your climate zone and construction requirements. For instance, in northern regions where you need attic insulation of R-49 to R-60, you might choose different materials than in milder climates.
The scientific measurement of these values occurs under controlled laboratory conditions, giving you precise data for comparison. However, you should note that real-world performance can vary by up to 20% from these laboratory values.
System R-Values
MaterialSpecific values combine with other building components to create system R-values. When you integrate various materials, their interaction becomes more complex than simple addition.
Your wall system, for example, includes not just insulation but also air films, sheathing, and structural elements. Thermal bridging through studs can reduce your effective R-value by up to 50% in some cases.
The scientific approach requires you to consider these interactions when calculating total thermal resistance. Air spaces between layers can either enhance or diminish performance, depending on their configuration.
This comprehensive understanding helps you optimize your insulation strategy by accounting for all components in your building envelope.
Effective R-Values
While laboratory measurements provide baseline data, you'll find that effective R-values reflect real-world performance. Environmental factors like moisture, temperature, and aging can significantly impact insulation efficiency.
Your insulation's performance varies with temperature, generally improving in colder conditions. This phenomenon means you might achieve better thermal resistance during winter months.
The installation quality dramatically affects performance, with poor installation potentially reducing efficiency by up to 30%.
A proper understanding of effective R-values helps you make more informed decisions about your insulation strategy, considering both theoretical and practical aspects.
Cumulative R-Values
Types of layered insulation can work together to enhance your overall thermal resistance. When you combine different materials, you can achieve optimal performance for specific climate challenges.
Your cumulative R-value calculations must account for all layers in your building envelope, including air films and cavities. This comprehensive approach ensures accurate performance predictions.
The scientific principle of thermal resistance addition allows you to stack compatible insulation types for enhanced performance, provided you maintain proper installation techniques.
Understanding cumulative R-values enables you to design more efficient and cost-effective insulation systems by strategically combining different
Factors Affecting R-Value Performance
After understanding the basics of R-value, it's crucial to explore various factors that can impact its performance:
- Temperature fluctuations and their effect on insulation efficiency
- Moisture content and humidity levels in the environment
- Quality of installation and proper fitting
- Density of insulation materials
- Air gaps and their impact on thermal resistance
Knowing these factors will help you optimize your insulation's performance and maintain its effectiveness over time.
Temperature Variations
On a fundamental level, your insulation's R-value performance can significantly change with temperature fluctuations. When temperatures drop below freezing, most insulation materials experience a 15-20% increase in their R-value. This occurs because colder air molecules move more slowly, reducing heat transfer efficiency.
Temperature Effects on R-Value
**Cold Conditions (Below 32°F)** | **R-value increases by 15-20%** |
---|---|
Hot Conditions (Above 90°F) |
R-value decreases by 10-15% |
Your insulation's performance can vary dramatically between seasons. During summer months, when temperatures soar, you might notice a decrease in insulation effectiveness as the material's R-value diminishes with higher temperatures.
The relationship between temperature and R-value isn't linear, and you'll find that different insulation materials respond differently to temperature changes. For instance, fiberglass insulation typically shows more significant R-value fluctuations compared to closed-cell foam insulation.
Recommended R-Values by Application
For optimal thermal performance and energy efficiency in different building applications, you need to understand the specific R-value requirements that will best serve your needs. The recommended values vary significantly based on building type, location, and specific application within the structure.
Residential Buildings
Little do most homeowners realize that proper insulation can reduce their energy bills by up to 15-20%. Your home's insulation needs vary depending on the specific area - your attic typically requires R-38 to R-60, while your walls might need R-13 to R-21. These values are based on extensive research and real-world performance data.
You'll find that in your attic, where heat loss is most significant, the recommended R-values are notably higher than other areas. For your walls, the requirements depend on the construction - if you have 2x4 walls, you'll need R-13 to R-15, while 2x6 walls require R-19 to R-21. Inadequate insulation in these areas can lead to significant heat loss and moisture problems.
Your floors and crawl spaces shouldn't be overlooked, as they typically need R-25 to R-30. These recommendations ensure that your entire home maintains a consistent temperature while maximizing energy efficiency. Proper installation is just as important as selecting the right R-value - even small gaps can reduce insulation effectiveness by up to 25%.
Commercial Structures
Little attention is often paid to the fact that commercial buildings have different insulation requirements than residential structures. Your commercial building's insulation needs are typically more complex due to larger spaces, different usage patterns, and varied heating/cooling demands.
You'll need to consider that commercial buildings often require higher R-values due to their size and occupancy patterns. The recommended values for commercial roofs typically range from R-20 to R-35, while walls might need R-13 to R-26, depending on your climate zone and building use.
Your choice of insulation in commercial spaces must also account for fire safety regulations and acoustic requirements. The combination of these factors often leads to layered insulation systems that can achieve R-values above 30 in critical areas.
Buildings with specific temperature control requirements, such as warehouses or data centers, might need even higher R-values. These specialized applications often require customized solutions that exceed standard recommendations to maintain precise environmental conditions.
Mobile and Vehicle Applications
Your insulation needs extend beyond traditional buildings - mobile spaces like campervans and RVs present unique insulation challenges. While these vehicles require similar attention to R-values as buildings, they often need specialized solutions due to space constraints and weight considerations. For example, this campervan insulation and ventilation guide explains that thin, high-performance materials like closed-cell foam can provide excellent R-values while maximizing limited space in vehicle conversions.
You'll find that mobile applications often require careful balance between R-value and practicality. The confined spaces in vehicles mean that even small variations in insulation thickness can significantly impact usable space, making materials with higher R-value per inch particularly valuable. These specialized needs often justify investing in premium insulation materials that might be cost-prohibitive in larger applications.
Your mobile structure's insulation strategy must also account for the dynamic nature of vehicle environments. Unlike stationary buildings, vehicles frequently move between different climate zones, making versatile insulation performance crucial for year-round comfort.
Climate Zone Considerations
Even the most well-designed insulation system must be adapted to your specific climate zone. Your location significantly impacts the R-value requirements, with colder climates demanding higher R-values to maintain comfortable indoor temperatures.
You'll find that in northern regions, your insulation needs might be up to 50% higher than in southern areas. The difference is particularly noticeable in attic insulation, where northern climates might require R-49 to R-60, while southern regions might only need R-30 to R-38.
Your building's exposure to wind, humidity, and solar radiation also affects the optimal R-value. These environmental factors can impact insulation performance, making it necessary to consider local weather patterns when selecting insulation materials.
This variation in requirements across climate zones highlights the importance of consulting local building codes and energy efficiency standards. Your specific location might have additional requirements beyond the basic recommendations.
Building Component Requirements
Now that you understand the basics, let's examine how different building components require varying R-values. Your roof and attic typically need the highest R-values, as they account for the most significant heat loss in most structures.
You'll find that walls have different requirements based on their construction and exposure. External walls facing prevailing winds might need additional insulation compared to protected walls, while basement walls have their own specific requirements.
Your windows and doors, though not typically associated with R-values, play a crucial role in the overall thermal performance. Modern double-pane windows can achieve R-values of
Tips for Optimizing R-Value
To maximize your insulation's effectiveness and achieve optimal thermal performance, consider these vital guidelines:
- Select appropriate R-value ratings for your climate zone
- Ensure complete coverage without gaps or compression
- Implement proper air sealing before insulation installation
- Consider layering different materials for enhanced performance
- Monitor and control moisture levels in insulated spaces
Proper Installation Techniques
Even the highest-rated insulation materials will underperform if installed incorrectly. You must ensure that your insulation fits snugly between joists, studs, and other framing members without being compressed, as compression can reduce R-value by up to 50%.
When installing batts or rolls, you should cut them precisely to fit around obstacles like electrical boxes, pipes, and wiring. Avoid leaving gaps or voids as these can create thermal bridges that significantly reduce overall insulation effectiveness. Your careful attention to these details can improve thermal performance by up to 30%.
You'll need to maintain consistent depth throughout the installation to achieve the rated R-value. For blown-in insulation, you should use depth markers and ensure even distribution. Proper installation can increase energy efficiency by 20-30% compared to poorly installed insulation.
Layering Strategies
Little do many realize that combining different insulation materials can significantly enhance thermal performance. You can achieve higher R-values by layering materials with complementary properties, such as combining fiberglass batts with rigid foam boards.
Your layering strategy should account for the specific characteristics of each material. For example, you might use a vapor-permeable material facing the interior and a more moisture-resistant layer toward the exterior. This approach can increase overall R-value by up to 40%.
When implementing multiple layers, you should ensure each layer is properly secured and maintains contact with adjacent materials. Gaps between layers can reduce effectiveness by up to 25%.
Installation of multiple layers requires careful planning and execution. You should stagger the seams between layers and ensure continuous coverage. This technique can provide superior thermal performance and reduce energy costs significantly.
Moisture Management
Strategies for moisture control are fundamental to maintaining insulation effectiveness. You must implement proper vapor barriers and ensure adequate ventilation to prevent condensation within insulated spaces. Moisture can reduce R-value by up to 40% if not properly managed.
Your moisture management approach should include careful consideration of vapor barrier placement. In most climates, you'll want to position vapor barriers on the warm side of the insulation to prevent condensation within the insulation material.
By implementing proper drainage planes and weather-resistant barriers, you can protect your insulation from both external and internal moisture sources. Effective moisture management can extend insulation life by 15-20 years.
Optimizing moisture control requires continuous monitoring and maintenance of your ventilation systems, vapor barriers, and drainage planes. This comprehensive approach can prevent up to 90% of moisture-related insulation failures.
Ventilation Considerations
Some of the most critical aspects of insulation performance relate to proper ventilation. You must maintain adequate airflow in attics and crawl spaces to prevent moisture accumulation while preserving thermal efficiency. Poor ventilation can reduce insulation effectiveness by up to 35%.
Your ventilation strategy should include both intake and exhaust vents positioned to create effective air movement. This balanced approach helps maintain consistent temperatures and reduces the risk of condensation.
When designing ventilation systems, you should calculate the required ventilation ratio based on your climate zone and insulation type. Proper ventilation
Step-by-Step Guide to R-Value Selection
Now, let's break down the systematic approach to selecting the appropriate R-value for your insulation needs. Key Selection Factors and Considerations
Factor | Consideration | |
---|---|---|
Climate Zone |
R-38 to R-60 for northern regions |
|
Building Component |
Walls: R-13 to R-21 |
Attics: R-30 to R-60 |
Cost Efficiency |
Optimal range before diminishing returns |
|
Material Options |
Fiberglass, foam, cellulose options |
Assessing Climate Requirements
For optimal thermal performance, you must first understand your specific climate zone requirements. Your geographical location significantly influences the R-value requirements, with northern regions typically requiring R-38 to R-60 for attic spaces, while southern zones might function effectively with lower values. You'll need to consider seasonal temperature variations in your area. The more extreme your temperature swings, the higher R-value you'll require. Your local building codes typically reflect these requirements, but they represent minimum standards rather than optimal performance levels. Your heating and cooling costs can be reduced by up to 40% with proper R-value selection. Analysis of your local climate data, including average temperature ranges and humidity levels, will guide you toward the most energy-efficient choice.
Evaluating Building Components
Little do many realize that different parts of your building require varying R-values. Your walls, attic, floors, and foundation each have unique thermal requirements based on their exposure and function within the building envelope. You must consider the existing insulation and construction materials when calculating your needs. Modern building science shows that proper insulation can reduce energy costs by 15-30% when applied correctly to all building components. Your building's age and construction type will influence your R-value requirements. Older buildings might require higher R-values to compensate for less efficient building materials and construction methods. For instance, you should know that your attic typically requires the highest R-value in your building, as it's responsible for 25-40% of your home's heat loss. When evaluating each component, consider its exposure to external elements and its role in your building's thermal envelope.
Calculating Required Values
Required calculations for your R-value selection must account for multiple factors. You'll need to consider the existing R-value of your building materials, including air films and air spaces, which contribute to the overall thermal resistance.
Your calculations should include an analysis of cost versus benefit. While higher R-values generally provide better insulation, there's a point of diminishing returns after R-38 in most applications.
You must factor in local building codes and energy efficiency standards when determining your required R-values. These regulations often specify minimum R-values for different building components in your climate zone.
RValue calculations become more complex when dealing with layered insulation systems. You'll need to add the R-values of each layer to determine the total thermal resistance, considering that proper installation can affect efficiency by up to 30%.
Material Selection Process
Clearly, your choice of insulation material will significantly impact your ability to achieve desired R-values. Different materials offer varying R-values per inch, affecting the thickness needed to reach your target thermal resistance. You must consider factors beyond just R-value when selecting materials. Moisture resistance, fire safety, and environmental impact should all factor into your decision-making process.
Pros and Cons of Different R-Value Solutions
Despite the various insulation options available in today's market, each R-value solution comes with its distinct advantages and drawbacks that you need to consider for your specific needs. Solution Comparison
**Fiberglass Batts** | \+ Cost-effective, widely available \- Can settle over time, requires careful installation |
---|---|
Spray Foam |
+ Superior air sealing, high R-value per inch - Expensive, requires professional installation |
Cellulose |
+ Eco-friendly, good sound dampening - Can settle, moisture sensitive |
Rigid Foam Boards |
+ Excellent moisture resistance, consistent R-value - Higher cost, requires precise cutting |
Mineral Wool |
+ Fire resistant, sound blocking - Heavier than alternatives, higher cost |
Reflective Barriers |
+ Effective in hot climates - Limited benefit in cold regions |
Natural Materials |
+ Environmentally friendly - Variable performance, limited availability |
High R-Value Materials
You'll find that modern high R-value materials offer unprecedented insulation performance, with spray foam leading the pack at R-6.5 per inch. When you compare this to traditional fiberglass batts at R-3.5 per inch, the difference becomes striking. Your choice of high R-value materials will significantly impact both initial costs and long-term energy savings. The latest polyisocyanurate boards, for instance, can achieve R-values of up to R-8 per inch, making them particularly effective for areas with space constraints. Your investment in high R-value materials might seem substantial initially, but the enhanced thermal performance can reduce your heating and cooling costs by up to 50% compared to minimum code requirements.
Final Words
As a reminder, your understanding of R-values represents a fundamental cornerstone in thermal efficiency and scientific measurement. When you evaluate insulation requirements for your specific needs, you'll find that the optimal R-value isn't merely a singular, universal number, but rather a calculated response to your geographical location, climate conditions, and specific application requirements. Your careful consideration of these factors will ultimately determine the effectiveness of your insulation strategy. Through your exploration of R-values, you've encountered the fascinating interplay between thermal resistance and energy efficiency. The scientific principles underlying R-values demonstrate that while higher numbers generally indicate better insulation properties, your pursuit of the highest possible R-value isn't always the most rational approach. Your investment in insulation should be guided by the law of diminishing returns, where you'll find that beyond certain thresholds (typically R-38 for most residential applications), additional insulation provides negligible benefits relative to the cost. When you apply this knowledge to your practical decisions, consider that your understanding of R-values empowers you to make evidence-based choices rather than relying on arbitrary assumptions. Your ability to interpret R-values within their proper context - whether for sleeping pads, wall insulation, or attic barriers - represents a triumph of scientific literacy over marketing claims. The empirical nature of R-value measurements provides you with a reliable metric for comparing different insulation options, enabling you to make informed decisions based on quantifiable thermal resistance rather than subjective assessments.